
We make science an art...
Metal Injection Molding
with in-house tooling & mold making

1330 W. Willow St. • Lafayette, LA 70506
(800) 598-5274
We can simply quote your part requirements or we can dive in and find manufacturing efficiencies to save you money. Working with ASH as a metal injection molding supplier, you will have access to MIM creativity and people who are not afraid to find manufacturing and design efficiencies for your metal injection molded parts.
Metal Injection Molding
MIM
Powdered Metal
MIM works similar to the other injection molding processes - powdered metal is combined with a binding material and then injected into a mold where it's left to form and curate. The end result is a metal part. The process is ideal for the short and long-run production of metal parts, especially those that are smaller in size and more detailed in terms of properties.
Here's a closer look at the MIM process:
-
Mixing and Granulating: The first step in the metal injection molding process is determining the material and feedstock that is going to be used to create the parts. (For more on material range, see the section near the bottom of this article.) Generally, this consists of fine powdered metals - a powder that is fine enough to create the features that are necessary. After the metal powder is determined, it's mixed with a thermoplastic binder (often which takes up 40 percent of the total feedstock), heated so that the metal grains bond with the binder and then fed into the injection molding machine.
-
Molding: The next step is the molding process, where the material is again heated and then injected into the machine for the molding process, which is the point where the part is created.
-
Binder Removal: After the part is ejected, the next step is to remove the binder. That's because the final part is about 20 percent larger than the intended end part. Hence, in order to get it to actual size, the binder needs to be removed.
-
Sintering: The final step in the process involves sintering, where the remaining binder is removed from the part and the metal is fused to create the part, the end result being a net shape or close to net shape final part. Further post-sintering operations may also be necessary to properly create the final part, which can add some further steps and complexities to the process.
Experience and talent is what you need if you want to make a successful, cost-effective metal injection molded parts (also known as MIM )

Custom MIM parts in complex or simple configurations for commercial and medical applications.
MIM produces net shape complex parts.
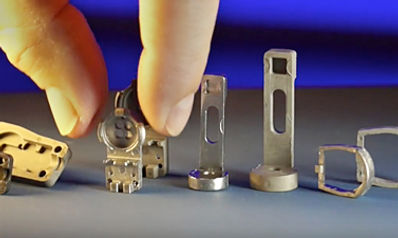
ASH specializes in medical devices and aeropsace Thermoset Silicone parts. You can also overmold with silicone to create seals and finishes.

Green part (back) is the injection molded part then fired to create net shape finished metal parts.
All in all, MIM is comparable to creating products from bar stock metal, both in terms of tensile strength and design capability. Here's a further look at the metal injection molding process and whether it's the right production process for your ASH™ part run:
Advantages
So what makes your part suitable for creation via MIM? To determine this, here's a look at some of the advantages of the ASH™ process:
-
Design Complexity: If you're satisfied with the design freedom you get from plastic injection molding but want to craft metal parts, then MIM could be right for you. That's because the two processes are quite similar in terms of design complexity - the main differences being that one produces plastic parts and the other metal ones. With MIM, cross holes, angle holes, splines, undercuts, side holes and grooves are all possible. Additionally, with MIM you can create whole parts that would often have to be created separately and assembled in post production.
-
Small Size: Remember, MIM uses very fine powders to create fully dense metal parts. Hence, the process is best for small parts, typically those that weigh between 0.1 and 250 grams.
-
Production Volume: MIM can be a very cost effective process, but only if the right number of parts are needed (not to mention if parts are the right size, as noted in the above point). Typically, the cost benefits are most noticeable and most worth it when part runs are between 10,000 and 20,000. Anything fewer than 10,000 and the potential cost savings from using MIM might not be evident at all.
-
Properties: As we've already noted, MIM is able to create fully dense or near fully dense metal parts when the process is complete, if the process is carried out correctly. It's particularly beneficial for parts that are too small or too detailed to machine out of bar stock. For comparison's sake, it's estimated that the part density is 98 percent via MIM, compared to 100 percent via conventional machining processes.
-
Economical: Unlike machining, MIM doesn't cut away existing metal - it uses only the amount of materials that is necessary to create the product. Nothing is wasted.
-
If your part meets some, if not all, of the above criteria, then MIM might be the production process for your part run. Talk with an ASH™ specialist to learn what's best for you.